TL;DR: Full Sheet Processing on Portable Workbenches
- Quick Answer: Yes, you can process full 4x8 sheets on portable workbenches with the right setup and accessories
- Key Requirements: 92"+ work surface, outrigger support, guide rail system, and 60-80 lbs total weight capacity
- Time Savings: 10-20 minutes per sheet vs traditional sawhorses setup
- Space Needed: 12' x 8' clear area for full sheet manipulation
- Best For: Contractors processing 5+ sheets weekly, cabinet makers, and serious hobbyists with space constraints
Why Contractors Are Switching
Processing full sheets of plywood or MDF on job sites has always been a nightmare. You're dealing with 70-80 pound sheets that flex, no stable cutting surface, and accuracy requirements within 1/16".
Traditional sawhorses with a door on top? You're lucky to get within 1/4" consistently.
The shift to portable workbenches designed for sheet goods is driven by three factors: setup time (5 minutes vs 20), cutting accuracy (0.004" vs 0.25"), and worker safety (stable platform vs wobbly setup).
Essential Specifications for Full Sheet Processing
Work Surface Requirements
A portable workbench needs specific dimensions to handle 48" x 96" sheets effectively:
Minimum length: 92 inches provides full support without overhang Width: 24-25 inches prevents tipping during crosscuts Height: 35-36 inches reduces back strain during extended work
The Dash-Board workbench hits these specs at 92.56" x 24.41" x 35.5", weighing 62 pounds. Compare this to makeshift setups that rarely exceed 72" and you understand why dedicated systems work better.
Weight Capacity and Stability
Full sheets of 3/4" plywood weigh 70 pounds. Add your track saw (15 pounds) and you need 100+ pound capacity with zero flex.
Key stability features:
- Adjustable legs for uneven terrain (found on 15% of job sites)
- Cross-bracing to prevent racking
- Wide stance (24"+ width) for lateral stability
The Outrigger System: Extending Your Reach
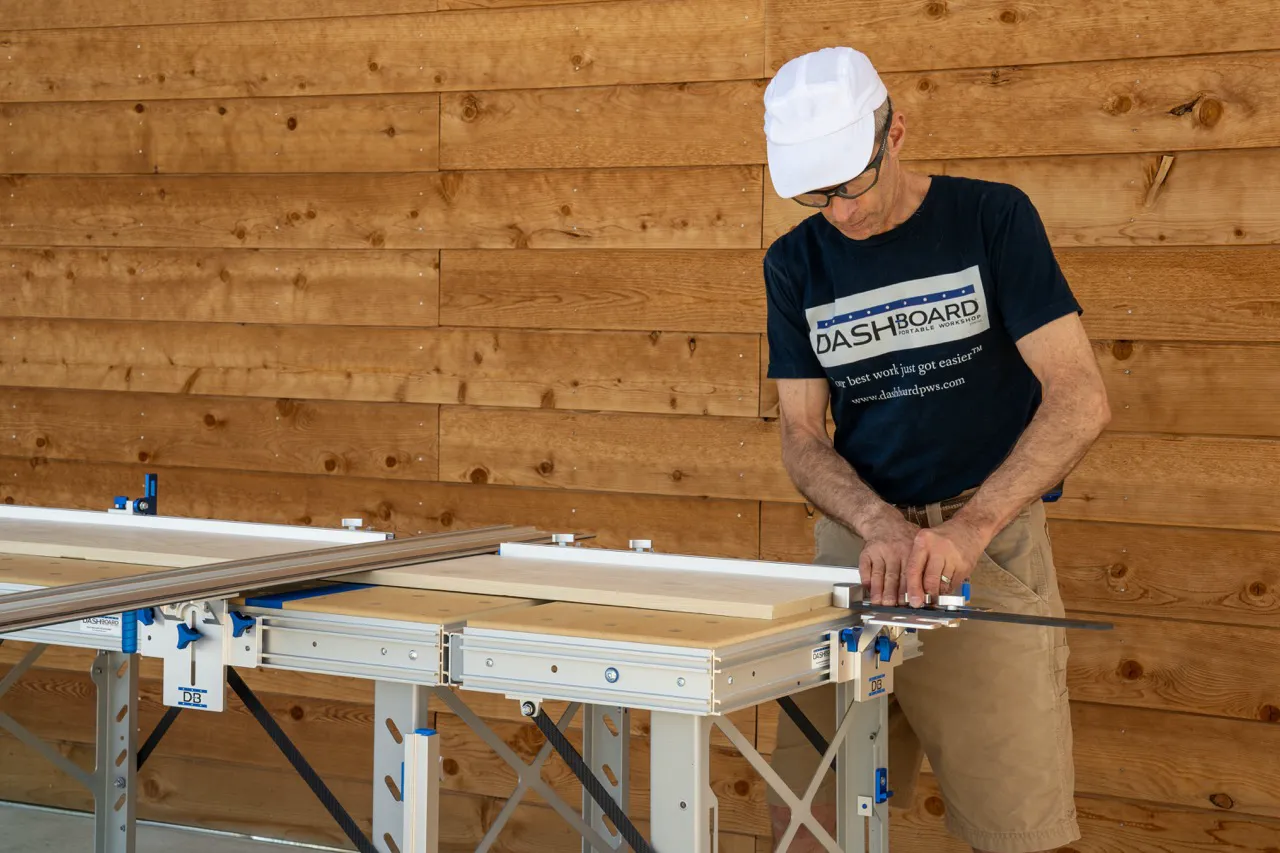
Processing full sheets requires support beyond the main work surface. Outrigger systems solve this by adding 24" of support on either end.
Without outriggers: Sheet hangs 24" off the end, causing flex and binding With outriggers: Full support allows clean cuts without assistant help
The math is simple: 48" sheet + 24" outrigger support = 72" of stable cutting surface. This eliminates the need for a helper, saving $25-40/hour in labor costs.
Guide Rail Integration for Precision Cuts
The Bracket System Advantage
Traditional guide rail setups require measuring and clamping for every cut. Modern bracket systems eliminate this:
Setup time: 30 seconds vs 3-5 minutes per cut Accuracy: Repeatable within 0.004" vs 0.125" variation Batch cutting: Set once, cut 20 identical pieces
The Dash-Board Guide Rail Bracket Set ($349) exemplifies this approach with tool-free installation and integrated alignment dogs.
Rip Capacity Mathematics
Full sheet rips require specific configurations:
- Standard setup: 50" rip capacity
- With Track Stars: 90" rip capacity
- With Outriggers: 100"+ rip capacity
This means you can rip a full sheet lengthwise (96") with the proper accessory configuration.
Crosscut Capabilities and Techniques
Crosscutting 48" requires different considerations than ripping:
Standard fence: 33.6" crosscut capacity With extensions: 48"+ crosscut capacity Critical factor: Material support on both sides of cut
The Track Star system addresses this by providing adjustable support at any point along the bench, preventing sheet sag during cuts.
The 2-Piece Top Innovation
Traditional workbenches get chewed up by saw blades. The 2-piece top with replaceable cut strip solves this:
Traditional: Replace entire top after 200-300 cuts ($150-300) 2-piece system: Flip cut strip after 500 cuts, replace after 1000 ($40)
This represents $360 annual savings for contractors processing 20 sheets weekly.
Real-World Time Comparisons
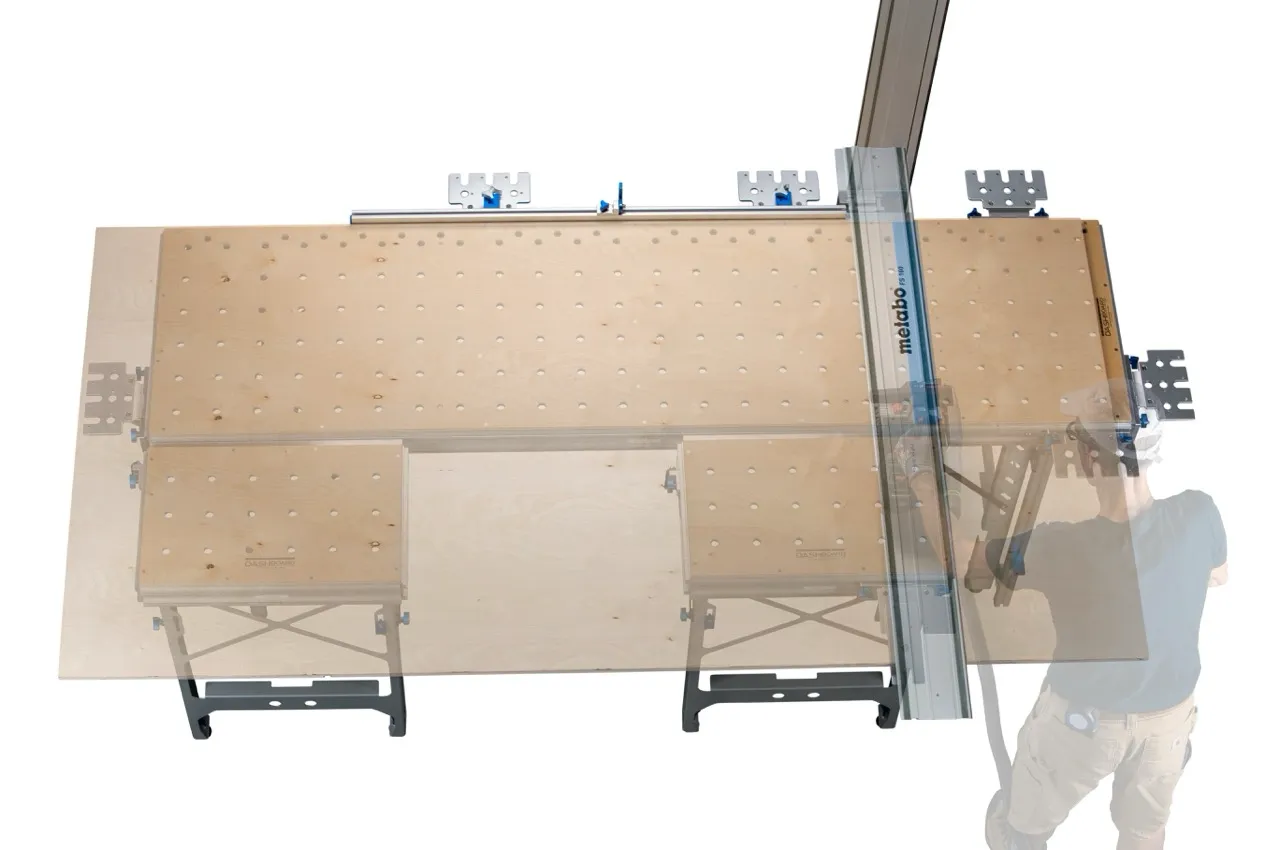
Based on contractor feedback processing 10 sheets:
Traditional sawhorse setup:
- Setup: 20 minutes
- Per sheet: 8 minutes
- Total: 100 minutes
Portable workbench system:
- Setup: 5 minutes
- Per sheet: 4 minutes
- Total: 45 minutes
That's 55 minutes saved per 10-sheet job, or $45-75 in labor costs.
Space Requirements and Site Logistics
Full sheet processing requires careful space planning:
Minimum clear area: 12' x 8' (allows sheet rotation) Ideal area: 14' x 10' (comfortable movement) Vertical clearance: 8' (for sheet flipping)
The modular design allows breakdown in 3 minutes for transport between cutting area and installation point.
Accessory Investment Analysis
Essential accessories for full sheet work:
At 20 sheets per week, full accessory ROI occurs in 5-6 months.
Learning Curve Reality
Contractor feedback indicates:
- Day 1: Basic cuts, 50% efficiency
- Day 3: Comfortable with system, 75% efficiency
- Week 2: Full productivity, finding new applications
The grid system takes adjustment but enables precision impossible with traditional methods.
Cost-Benefit Analysis for Different Users
Professional contractors (20+ sheets/week):
- Investment: $3,000-5,000 complete system
- Time savings: 15 hours/month
- ROI: 4-6 months
Serious hobbyists (5-10 sheets/week):
- Investment: $1,500-2,500 basic system
- Main benefit: Precision over time savings
- ROI: 12-18 months
Occasional users (<5 sheets/week):
- Traditional methods remain cost-effective
- Consider rental options for large projects
Practical Implementation Timeline
Week 1: Learn basic setup, practice straight cuts Week 2: Master grid system, add first accessories Month 1: Integrate into standard workflow Month 2: Explore advanced techniques (angles, tapers) Month 3: Full productivity with all accessories
FAQ: Full Sheet Processing
Can I process sheets larger than 4x8?
Yes, with dual bench setups you can handle 5x10 sheets. Connect benches end-to-end for 16' capacity.
What's the minimum accessory setup for sheets?
Guide rail brackets ($349), Track Stars($299/pair), F1 Fence ($129) and F2 Fence ($189), Spiral Dogs ($49), The Wingman ($59), and one outrigger ($550) enable basic full sheet processing.
Is the system overkill for 10 sheets monthly?
For precision work, no. For rough framing cuts, consider simpler solutions.
How does it compare to track saw + foam?
3x faster setup, 10x more accurate, eliminates foam waste ($50/month savings).